SERIES II,
1977
The original Series I rockers of 1973
were essentially unchanged when the Series II rockers were made 4 years later.
The only difference was that they incorporated Torrington Needle bearings, where
the Series I used a bronze bearing to work with the Ford .700" diameter NASCAR
shaft. Only 5 sets were made; four of these were used
solely on Jim's own BOSS engines. Although it was 4 years after the first Series
1 rockers were made before the Series II came out, they were in the pipeline
long before that, so there was no urgency to make more of the Series I rockers.
|
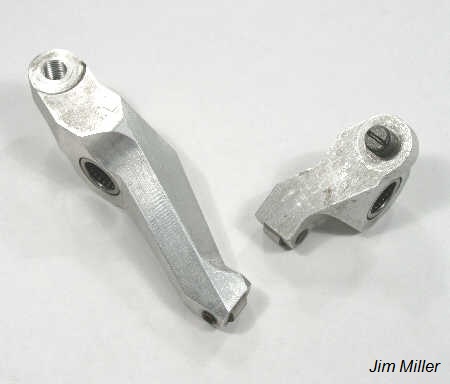 |
CLICK PHOTO
FOR SERIES III
The
1977 Series II BOSS rockers were machined from solid 7075-T6 Billet
Aluminum and fitted with Torrington needle bearings. Specially made
shafts that copied the NASCAR design, but incorporated a 5/8" diameter
were used in lieu to the .700" NASCAR dimension. Original NASCAR
stands were retained and modified to accommodate. Precision ground
steel plates nearly 1/4" thick were made to elevate the rocker as
needed to establish MID-LIFT geometry, first developed on the Series I
model in 1973.
Little
emphasis on pretty, shiny anodized surfaces was used, but they were
light, strong and safely allowed the engine up to 9,300 rpm, an
unheard of value for a big block in 1977. Repeat NHRA World Champion
Bob Glidden contracted several sets in 1979 when he switched from the
351 to a destroked BOSS 429.
|
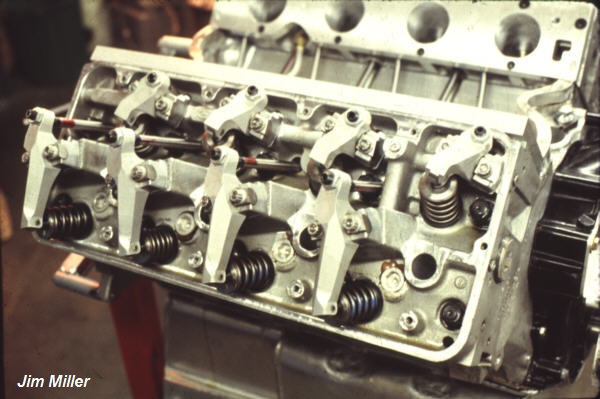 |
Lee Farrell's Ford Truck Pull engine (ca 1981); America's 1st Aftermarket
Aluminum BOSS block. |
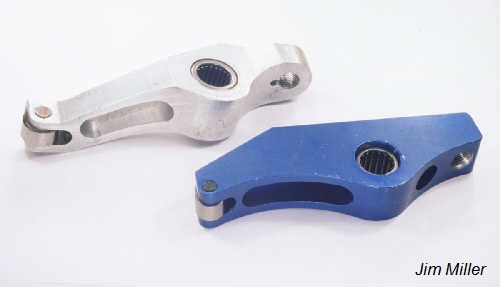 |
By 1980 or
'81, Jesel came out with his straight beam version of a rocker for the
BOSS engine and used the same bottom side ball mill lightening copied from
Miller. His early pieces added a second ball mill plunge on the back side
of the shaft bore, which proved fatal. That step was dropped.
|
The JESEL exhaust rocker for the BOSS
429, is rotated from the Ford mounting pad to "straighten up" Ford's deliberate
rotation and compound geometry, which balanced side thrusts back and forth
during the opening and closing cycle. JESEL'S change required welding and
machining, using quaint little steel blocks with dowel pins that serve as a jig,
but were (and are) very inaccurate as designed to be used. The process destroyed
the OEM mounting, making going back nearly impossible, or at least impractical.
What no one seemed to understand was the result of such a change was a bias side
load placed entirely in one direction, making harmonic control in the very long
exhaust pushrod (nearly 11 inches) impossible as well. The Miller system
maintained the Ford rotation, understanding it wasn't simply "to fit" around the
ports. Unfortunately, JESEL's compromise got copied by well known engine
builders and head manufacturers trying to resurrect a vague semblance of this
great engine; and thus, the problems. JESEL's answer for an intake rocker was to
use his Big Block Chevrolet rocker, even though its design geometry isn't
even close. The BOSS engine is the most susceptible of any American OHV engine
to optimum valve train geometry, and when any compromises are made -- the
detriment is even greater.
|
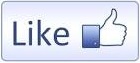

MILLER MID-LIFT™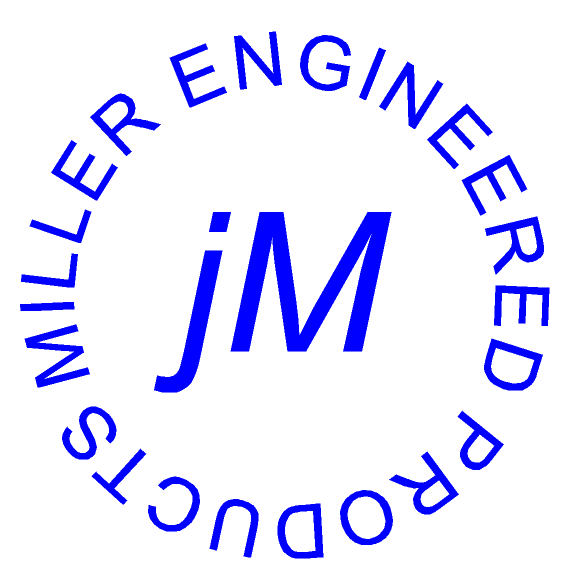 The Standard By Which All Is Measured!™
954-978-2171 MillerRockers@aol.com
MID-LIFT™, PRO-SHAFT™ & PRO-STUD™ are JM Miller Trademarks; Copyright © MMIII~MMXXIV
| |